IBARMIA
TECH-CYCLES
ADVANCED MANUFACTURING
Active assistance to the machining process.
SERVICE TECHNOLOGY
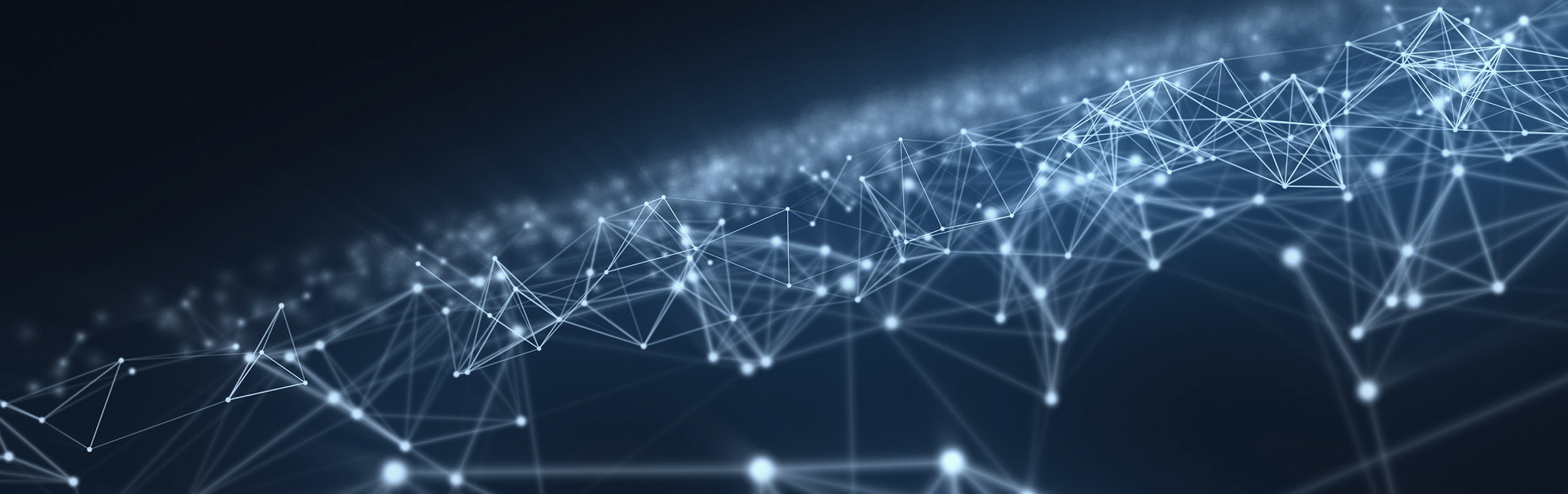
IBARMIA developments integrated in the machine CNC for advanced assistance and optimization of production processes.
Technological cycles
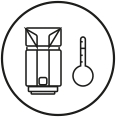
Electrospindle compensation
The compensation of thermal drift of the main spindle is designed to compensate the thermal drift of the Tool Centre Point (TCP) due to thermoelastic deformation of the main spindle.
Main features:
- Direct and indirect measurement of thermal drift of main spindle.
- It compensates the thermal drift of the electrospindle as a function of the temperature of the front bearing of the spindle.
- Improves machine accuracy up to 0,02 mm.
- Applies to all electrospindles and all IBARMIA machines.
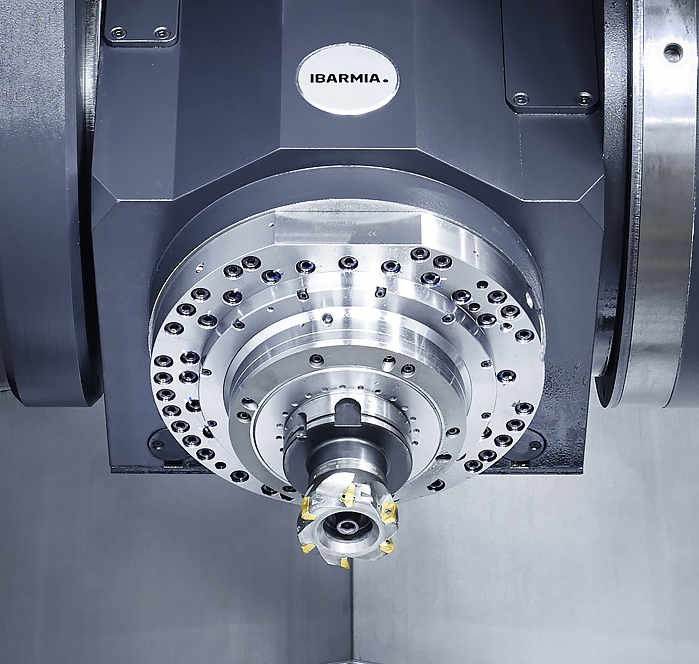
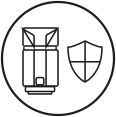
Electrospindle protection
This smart equipment has been designed to detect at very early stage abnormal situations and disturbances that may affect the lifetime of main spindles. This equipment will also take decisions for minimizing the effects of those disturbances and will also monitor the condition of spindle bearings in a continuous manner.
Main features:
- Control Monitoring of spindle imbalance during idling conditions and automatic warning for the case of imbalance values that are above predefined values at specific balance grades.
- Automatic stop of spindle feed axis for the case of abnormal vibrations above security threshold values.
- Continuous diagnostic of the state of spindle bearings for preventive maintenance purposes.
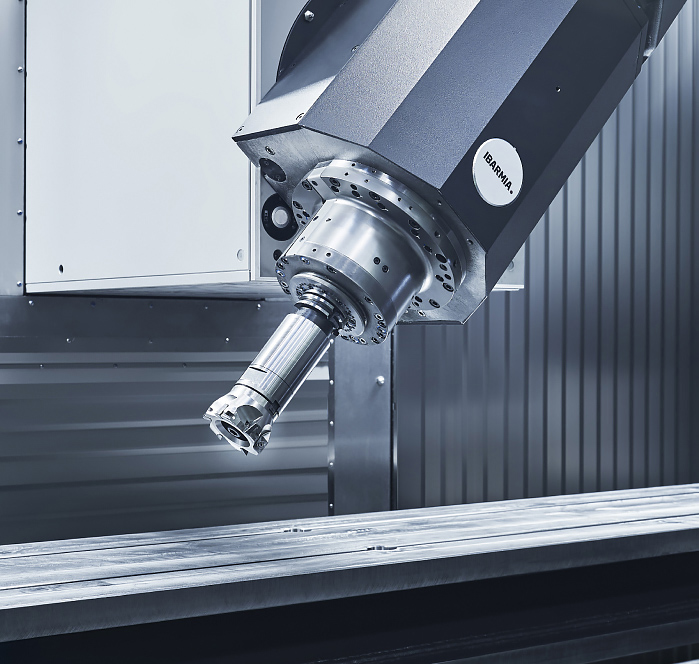
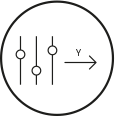
Y axis autotuning
This application is aimed to maximizing the position loop bandwidth for the case of variable moving masses placed on mobile tables.
Main features:
- Automatic measurement of axis weight for every notable change in the mass on moving tables.
- Automatic adjustment of velocity and position control gains for maximized position loop bandwidth according to the specific values of mass, inertia ratios and natural frequencies in the feed drive.
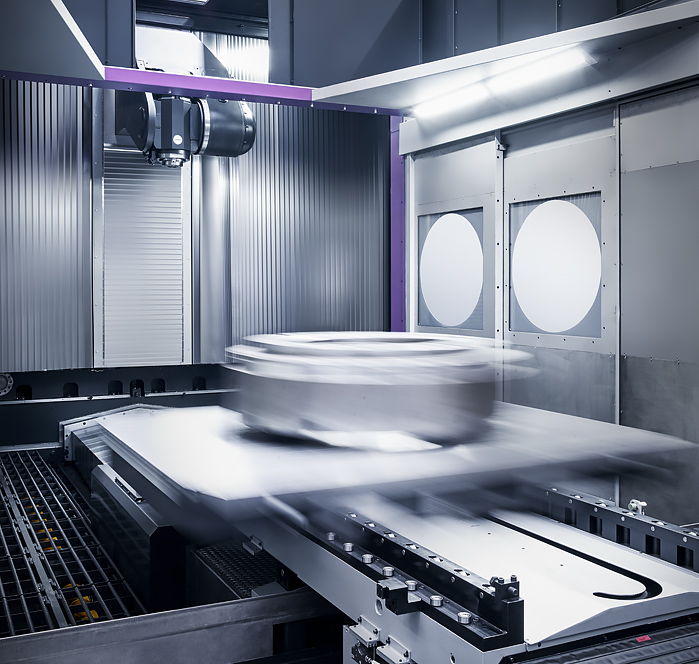
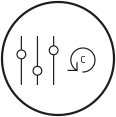
C axis autotuning
This automatic tuning procedure is aimed to maximizing the position loop bandwidth for the case of variable moving masses, placed on rotary tables.
Main features:
- Automatic measurement of axis inertia for every notable change in the mass on rotary tables.
- Automatic calculation of natural frequencies and inertia ratios by means of motor consumption signals.
- Automatic limitation of maximun rotational speed of moving table depending on workpiece weight, for axis protecion.
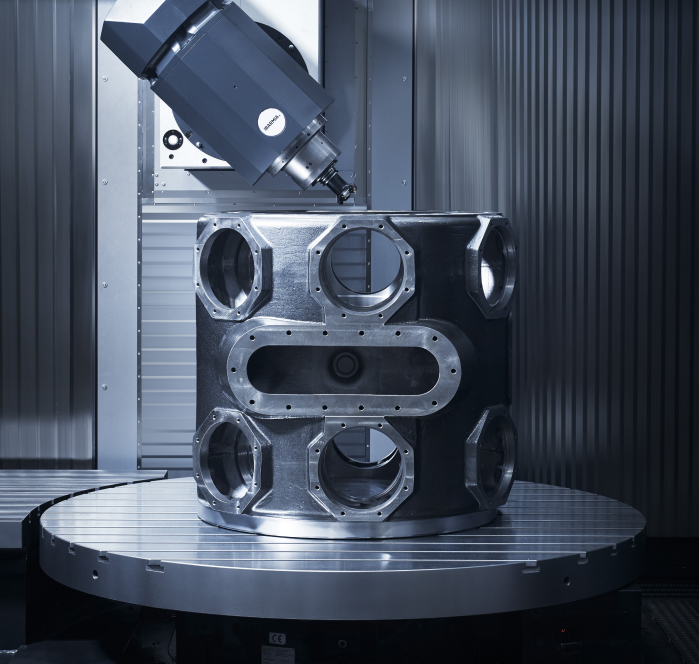
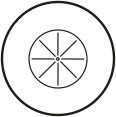
Residual unbalance check
Unbalance reduces the lifetime of the bearings and other components, produces noise and may be a safety risk; the Rotatory Axes Unbalance Compensation (RAUC) enlarges the life and the safety of your machine. Accelerometers located on the axis detect static, coupled and dynamic unbalance and fires an alarm that stops the spinning of the axis.
Main features:
- Static, coupled and dynamic unbalance detection.
- Mass distribution detection.
- Balancing mases weight and location suggestion for rotary tables.
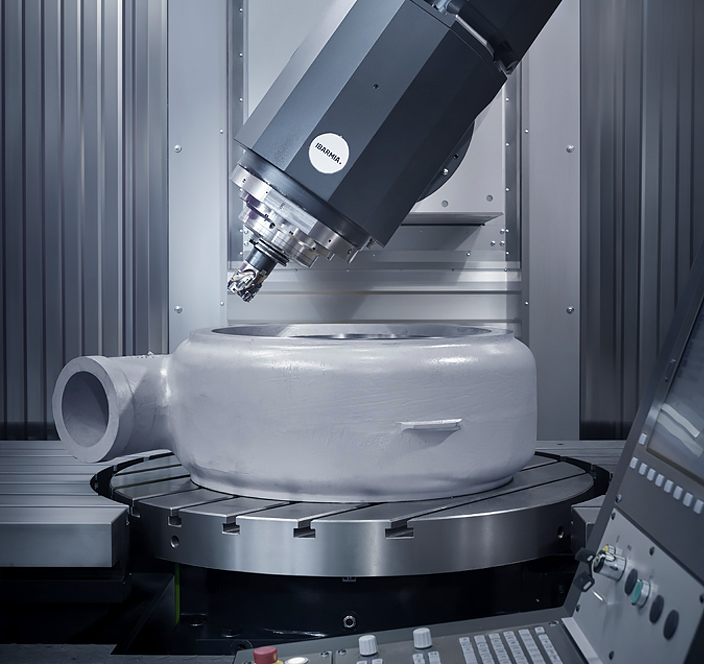
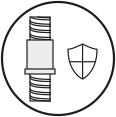
Ball-screw protection
The ball-screw protection control aims to protect the ball-screw from preload losses, vibrations and excessive temperatures. By the integration of a sensorized nut, it is possible to monitor and record the ballscrew control parameters continuously. Regarding the data collected, it is possible to check if the ball-screw is working correctly. In addition, it has integrated a ball-screw health check cycle for predictive maintenance that enables the early detection of failures.
Main features:
- Integration of sensorized ball-screws.
- Monitoring and recording of spindle control parameters.
- Predictive spindle maintenance.
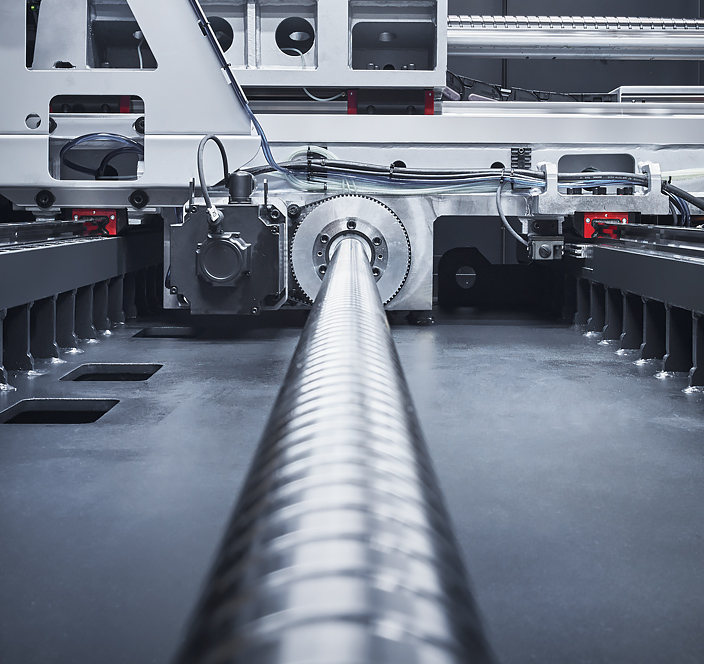
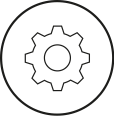
Gear machining
The gear machining is designed to support machine operators to program gear machining strategies in a simple and quick way. The interface requires the basic geometrical features of the gear (diameter, module, angle, length, etc.). With a conversational programming method, the CNC code is generated automatically, which implies a significantly reduced programming time. This type of programming is used in gear Hobbing and the gear Skiving.
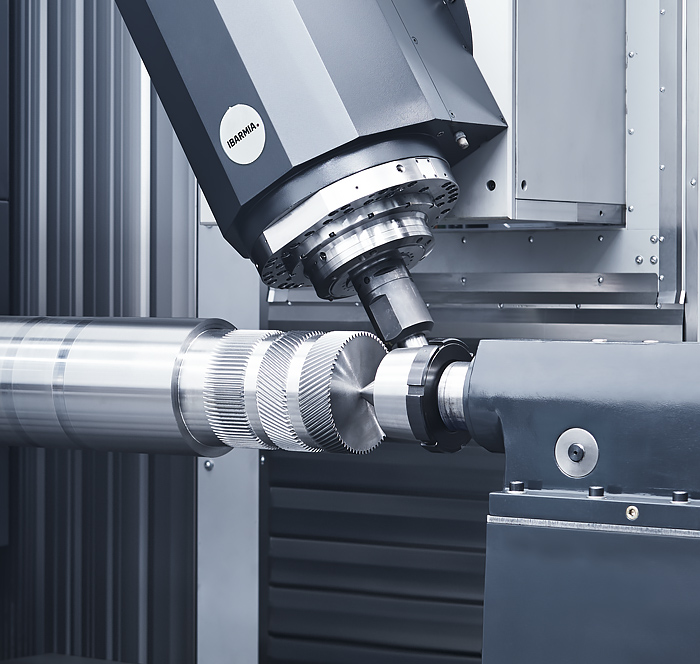
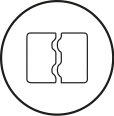
Mould pack
The mould pack consists of adjusting the machine dynamics for machining parts that involve roughing, semi-finishing and 5-axis surface finishing processes with the aim of optimising the ratio between speed and precision according to the type of work to be carried out.
Main features:
- Optimization of mould machining.
- The mode is chosen: roughing, semi-finishing or finishing. In the case of roughing it is optimized in time and in case of semi-finishing in surface quality.
- For each case, the variables to be modified are studied and a more precise optimization is made.
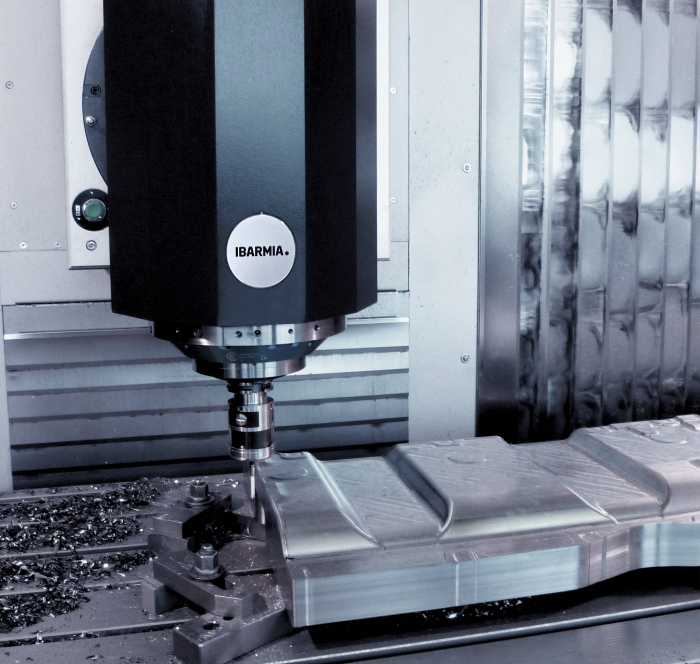
CONTACT US
Complete the form and tell us the reason for your inquiry so we can help you.
You decide
“Ibarmia makes the machine following your needs”
Contact with IBARMIA for further information
Contact us