New
SUBCONTRACTOR 2G TOOLING GETS NEW CUSTOMERS THANKS TO THEIR NEW IBARMIA ZVH 45/L3000 STAR MACHINE
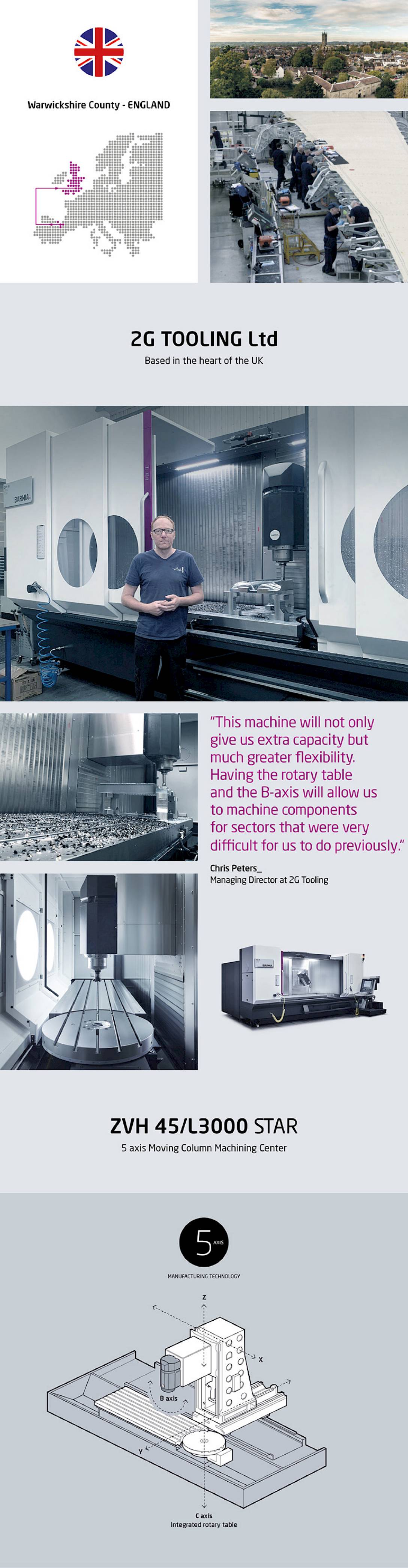
The English 2G Tooling Ltd offers a complete service from subcontract machining through design and manufacture. To expand the scope of its toolmaking capabilities, it recently purchased a large bed 5-axis IBARMIA machining center from Dugard, and even before the machine was fully installed, 2G Tooling just got its first order from a new aerospace customer.
Located near the major automotive OEMs in Warwickshire, 2G Tooling has rapidly built a prestigious reputation for manufacturing everything from fly press tooling through to large drawn tools, and specialization in precision press tooling, jigs and fixtures has carved a niche for 2G Tooling. Its work is mainly focused on the automotive industry, and during these las years the activity of the company was affected by the complicated situation in this sector.
In order to survive, they definitely needed to enter new sectors, but the England based company realized that their small machines were limiting their toolmaking capacity, so it was really difficult to enter new sectors such as the aerospace one.
The tools they were using had an overhang of 100-150 mm, which lead to a quite poor stability of their tooling, directly compromising the tool life and the subsequent high costs on cutting tools. This high overhang was also causing poor surface finishing, requiring long polishing times which were extending their lead times.
Talking about lead times, the English subcontractor was having long lead times with certain features such us making holes in the sides which needed to be done in three or four setups.
With all these problems in hands, 2G Tooling nocked the door of Dugard, CNC machine importer for UK and Ireland, and together they found the solution to help them expand the flexibility and capacity of their business. They needed a flexible machine that would offer them high capacity, and Dugard presented them the IBARMIA ZVH 45/L3000 STAR 5-axis machining center with a 3 m bed, a travelling column, +/-105-degree B-axis, a rotary table, and a capacity for up to 6-tonne workpieces on the bed.
The machine and its characteristics perfectly suited their needs, but they did not know the IBARMIA company, and there were running hard times for traveling. They decided to do a Zoom meeting with the factory in Azkoitia where the machines are manufactured, and they found a family-based company with a custom-tailored set-up that really cares the customers. After this meeting, the decision to buy the machine was taken.
“The difference between Ibarmia and what I have seen before from most mass-produced machine manufacturers is a bespoke set-up and family ethos of the business. You could actually see each machine going through production with more time and care being spent on each machine that is bespoke to the individual customers.”
Chris Peters, Managing Director at 2G Tooling
Once the machine arrived at the factory in Warwickshire, there were a few tipping problems during the installation, but Dugard offered an impeccable service giving a fast solution straight away. Chris Peters recognizes that “During the installation nothing goes 100% smoothly, but having that backup and that confidence, is just all you can ask for.”
During the first week while the machine was still being installed, 2G Tooling accepted an order from a new aerospace customer for machining long parts that before were not able to machine.
The machine installed at 2G Tooling incorporates the latest generation Heidenhain TNC640 HSCI CNC control system, on-machine probing, linear glass scale feedback on all axes with pre-loaded rolling shoes and a 40 position ATC. The new installation also provides 40m/min rapid feed rates, through coolant spindle, swarf conveyors and much more.
The IBARMIA ZVH 45/L3000 STAR provides a spacious 3m by 800 mm by 800 mm in the X, Y and Z-axis with an 800 mm diameter integrated rotary table that has a 1100 mm swing and this not only enhances flexibility for the company, but the integrated table also demonstrates astounding rigidity and stability for 5-axis machining. The ability to machine large parts in full 5-axis will significantly reduce secondary set-ups and lead times for 2G Tooling whilst the on-machine probing system will provide confidence that every part coming off the machine will be machined to impeccable precision levels without secondary set-ups.
With a BT/CAT 50 spindle taper and 27/39 kW of spindle power, the high torque 12.000 rpm spindle also demonstrates an exceptionally stable and powerful platform for heavy material removal rates and extended cutting tool performance. The English company has reduced the overhang of tools from 100-150 mm to 30 to 50 mm, improving the stability of their tooling, surface finishes and subsequent improvement of their tool life, faster cycle times, reduction of costs on cutting tools and even better quality of the products.
2G Tooling has gained capacity (up to 6 tons on the bed and 1.5 tons on the rotary table), and the fact that larger dies and workpieces can now go straight on the rotary table to be 5-axis machined, will open up 2G Tooling to new markets. “It’s all flexibility!” Says Chris.
SUBSCRIBE TO OUR NEWSLETTER
Subscribe to our newsletter to keep up to date with all our news.
SUBSCRIBE TO OUR NEWSLETTER
01